Fiberglass Reinforced Plywood Sandwich Panels
Fiberglass reinforced plywood panels are a high-strength, impact-resistant material that consists of 2 pieces of FRP sheets and plywood and is formed into FRP plywood panels. They can withstand great pressure and have the advantages of both FRP and plywood and are widely used in various applications.We work as a professional supplier for you.
We support customized production, OEM/ODM, and finished products such as trailers, carriages, and motor homes.
Product Description:
Fiberglass reinforced plywood panel structure: 2 layers of fiberglass sheets as exterior, core of plywood, formed by laminating 7 to 13 layers of thin wood.
Composite-box has 20+ years experience in producing premium fiberglass plywood panels for truck applications. Although plywood panels are a high-strength material, they are not waterproof, are prone to rot, and have many disadvantages. Nowadays, with FRP skin, they are able to be waterproof, scratch-resistant, rot-resistant, and UV-resistant, among other benefits. Options like stainless steel faced plywood also enhance durability for specific applications. These features make our <a href=”#”>fiberglass plywood panels</a> the ideal choice for truck applications.
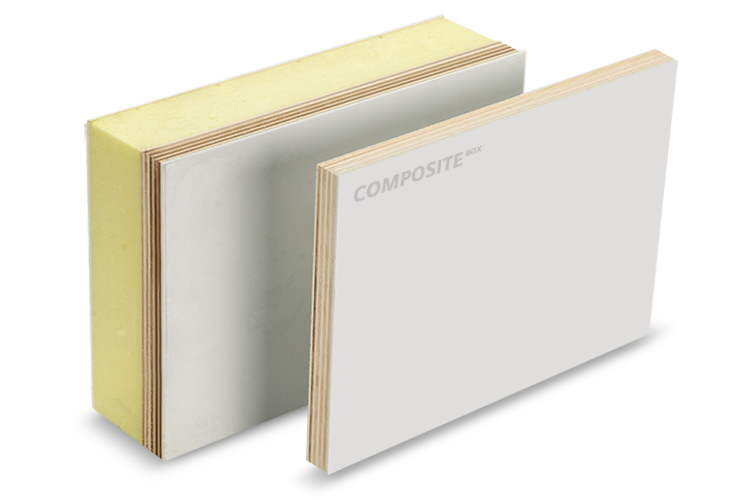
customization
We support product customisation and can produce different thicknesses on request, from 9mm to 22mm, lengths up to 12m and widths up to 3.2m. Customized FRP patterns and colours are available, as well as different skin finishes, and non-woven fabrics can be added to enhance adhesion. Sourcing fiberglass reinforced plywood, composite box is the best choice.
Product Advantages
Application

Fiberglass Roofing and Partitions on Plywood
Used for roofing, partitions and wall panels. Thickness in 10~50mm, waterproof and UV resistant, suitable for mobile homes, container homes, providing long lasting protection.

plywood fiberglass aquarium
Waterproof and pressure resistant, can be made into a large aquarium. The water body can reach 500L, durable for more than 20 years.

Fiberglass Plywood Cattle Shed
Thickness 10~30, waterproof and moisture-proof, suitable for wet environment, protect livestock, corrosion-resistant, not easy to be damaged by cattle.
Structure of fiberglass plywood

plywood
plywood is multiple layers of different thin wood slices laminated with adhesives to achieve high strength properties and is highly resistant to compression, maximizing the use of wood.
FRP Fiberglass sheet
PET (polyethylene terephthalate) is chemically stable, is recognized worldwide as an environmentally friendly recyclable material, consists of a closed cell structure, is waterproof and moisture resistant, and is the ideal material for many applications.
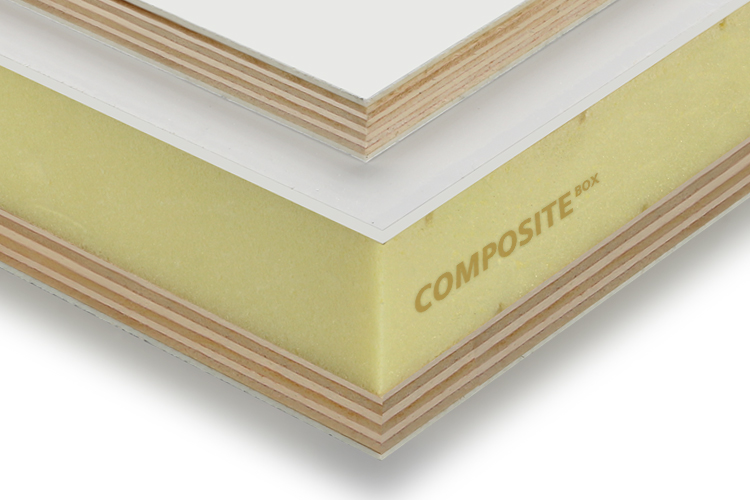
Composite Box
Application of fiberglass reinforced polywood panel :
FRP sandwich panels can be used mainly in scenarios that need high strength.
Product Parameters
Attribute | Specification/Value |
---|---|
Skin Thickness | 1.5 mm |
Core Thickness | 11 mm |
Areal Density | 1 Kg/m² |
Flexural Strength | 36.966 MPa (Max Load: 2770.659N, Sample Size: 300x100x14 mm) |
Compressive Strength | 13.053 MPa (Max Load: 2770.659N, Sample Size: 60x60x14 mm) |
Skin Material | FRP (Fiberglass Reinforced Plastic) or CFRT (Continuous Fiber Reinforced Thermoplastic) |
Core Material | Plywood (Poplar, Pine, Eucalyptus, Oak, etc.) |
Surface Treatment | Gelcoat FRP (Thickness: 0.7–5.0 mm) |
Composite Method | Eco-friendly adhesive |
Thickness Range | 5–50 mm |
Length Range | ≤12000 mm |
Width Range | ≤3200 mm |
Comparison of FRP skinned plywood and pure plywood performance
Item | Strength | Waterproof Performance | Fire Resistance | Surface Smoothness | Expected Lifespan | Moisture Resistance | Thermal Insulation |
---|---|---|---|---|---|---|---|
FRP Skin Plywood | Excellent | Excellent | Average | Smooth | Long | Good | Excellent |
Pure Plywood | Average | Poor | Poor | Rough | Short | Poor | Average |
why choose us?
Customer Satisfaction
Insisting on high quality products and servers, centered around customer experience
Quality Assurance
We strictly control every production process to bring reliable quality assurance to our customers.
Advanced Production Line
The world’s top production line ensures product precision and efficiency.
Customization
We provide 100% customization, making orders less difficult.