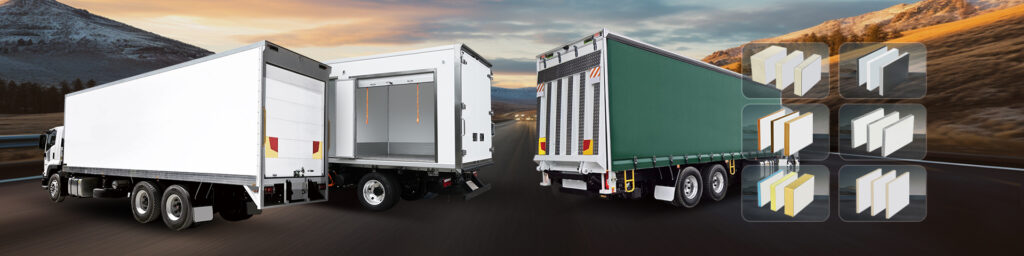
Stainless Steel/Galvanized Steel Foam Sandwich Panel Suppliers
About steel foam panel
Stainless Steel and Galvanized Steel Foam Sandwich Panels use either stainless or galvanized steel. They have a core made of waterproof, insulating, and strong rigid foam. Laminated together by high adhesive polyester glue. They are impact resistant, oxidation resistant, and corrosion resistant. Stainless steel stands out from other sandwich panels. It is ideal for high-strength uses. This includes building facades, decorative panels, trucks, and camper vans.
Galvanized steel performs similarly to stainless steel. It has great corrosion resistance. A layer of zinc coats its surface to prevent rust. It is also called the hot-dip galvanizing process. And it is suitable for use in a variety of harsh environments.
Features:
- Use of 202/304/316 austenitic stainless steel, or galvanized steel (aluminum-zinc plated steel sheet, pre-painted aluminum-zinc plated steel sheet).
- A wide range of foam cores is available.
- Surface coating: PE, PVDF
- Thickness: 8–120 mm
- Width: 1200–2440 mm
- Length: less than or equal to 12,000 mm
- Skin thickness: 0.2–5 mm; galvanized steel skin: 0.2–6.0 mm
- Type of sequins: normal, small amount, no sequins

Product Description:
Stainless steel and galvanized steel perform exceptionally well. They show high strength in building facades, floors, decorative walls, and more. Stainless steel lasts a long time. It resists oxidation and doesn’t deform or age easily. So, its service life can exceed 30 years.
It also has a strong ability to adapt to the environment. It can handle temperatures from 40 ℃ to -30 ℃. It resists thermal expansion, contraction, and deformation well. Its structural stability remains strong. Overall, it is more durable than traditional skin materials such as glass fiber reinforced plastic and aluminum, and it can reduce business costs and increase long-term benefits.
- Can be used as a fireproof material.
- Non-rusting
- Highly decorative
- Resistant to high and low temperatures.
- High strength, not easily deformed.
- Easy to clean.
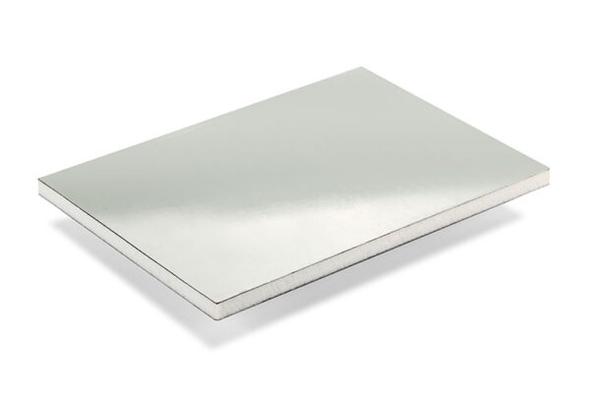
Structural performance:
Composite Box prioritizes the quality of every composite panel. We ensure that its strength remains strong over time. Our high-precision laminating technology, used with high-pressure presses, enhances the composite’s performance. This means it won’t lose its effectiveness later on.
Sandwich panels are made with top-grade stainless steel and galvanized steel skins. They also include rigid foams. You can choose from polyurethane, XPS, polyester, PVC, and more foams. Stainless steel skins can be used in a variety of ways to improve surface properties. For example, you can use polishing, brushing, sandblasting, or PVD coating. These methods offer versatility and various appearance effects.
- Polishing: Mechanical and chemical treatments can smooth the surface and boost gloss.
- Brushing: This process uses special tools to create a smooth pattern on stainless steel. It helps improve slip resistance and makes the surface look better.
- Sandblasting: Abrasive material is sprayed on stainless steel. This creates a rough, even surface that helps improve adhesion.
- PVD Coating: Physical vapor deposition technology improves corrosion resistance and durability.
Parameters:
Type | Tensile Strength (MPa) | Compressive Strength (MPa) | Hardness |
Galvanized steel | Generally 60 – 80 | Generally 30 – 50 | Generally 150 HB |
304 stainless steel | 520 | Generally greater than 205 | Generally 187 HB |
316 stainless steel | 520 – 620 | Generally greater than 215 | Approximately 180 – 200 HB |
410 stainless steel | 410 – 540 | Generally greater than 205 | About 183 HB in annealed state, and can reach above 50 HRC in quenched and tempered state |
Related Product
Fiberglass XPS insulation panel
Fiberglass XPS insulation panels use fiberglass as a skin, have better impact resistance, can be used in high-frequency scenarios, offer corrosion resistance, and have a long life.
Continuous fiber XPS insulation panel
Continuous fiber, also known as CFRT or new FRP, is suitable for scenes with higher requirements for elasticity.
Metal XPS insulation panel
Metal skin is durable and more protective, generally using color-coated coils or steel coils.

Application
What is steel foam panels used for?
Stainless steel foam panels are used in situations needing lightweight, sanitary, and strong materials. They offer thermal and acoustic insulation, resist corrosion, and deliver high performance.
- Chemical Laboratory
- Refrigerated truck series
- Dry van series
- Hospital
- Central kitchen
- Aseptic Room
why choose us?
Customer Satisfaction
Insisting on high quality products and servers, centered around customer experience
Quality Assurance
We strictly control every production process to bring reliable quality assurance to our customers.
Advanced Production Line
The world’s top production line ensures product precision and efficiency.
Customization
We provide 100% customization, making orders less difficult.