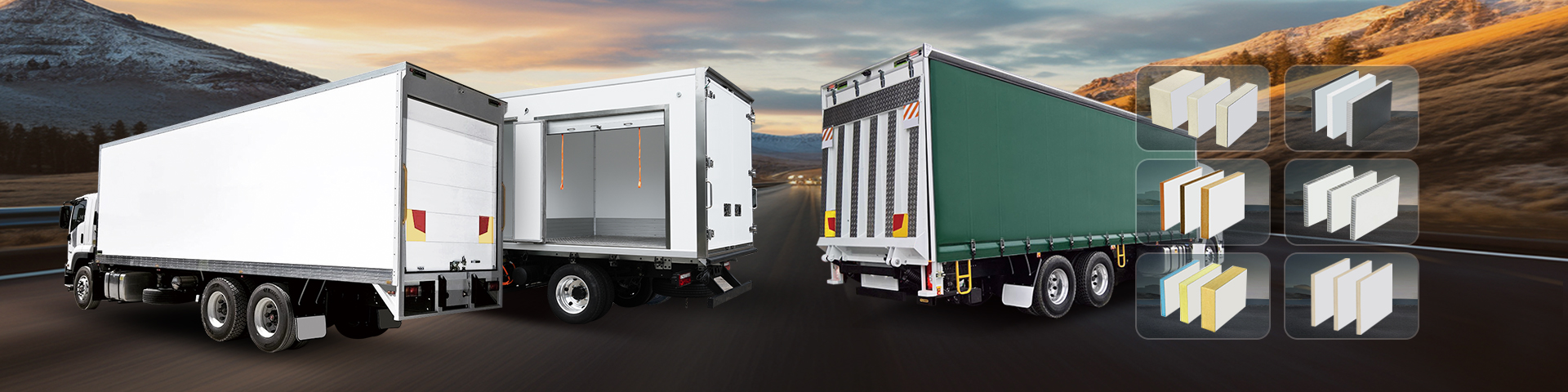
fiberglass XPS Foam sandwich panels manufacturer
what’s fiberglass XPS sandwich panels?
Fiberglass XPS sandwich panels are made from a combination of fiberglass skins and XPS foam with a flat surface. Adopting a high-pressure curing process, they combine the common advantages. They have the characteristics of UV resistance, good heat preservation, high strength, and rigidity. They can replace traditional composite materials.
We can provide you with customized CNC machining, embedded reinforcing materials, and better UV resistance.
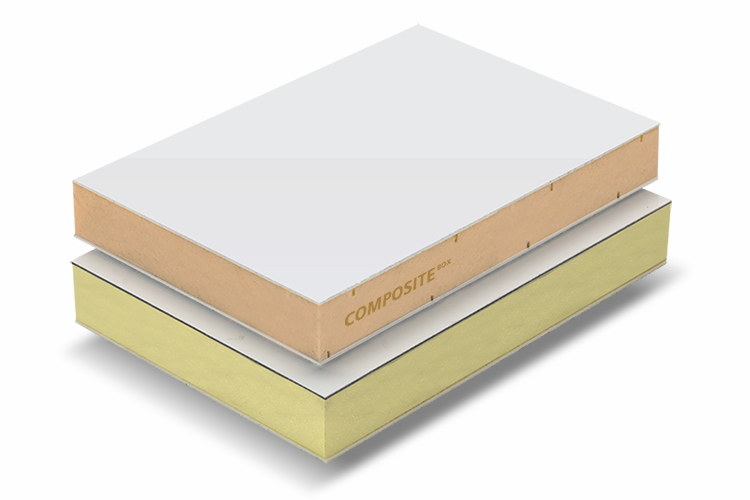
Product Description:
Composite-box is a manufacturer specializing in fiberglass XPS sandwich foam panels. Its FRP skins are gel-coated and bonded using adhesives that do not come off. The core uses XPS (extruded polystyrene insulation), which is a continuous process that creates a closed-cell structure that is 99 percent waterproof. The surface is smooth, and the density and thickness of the foam core can be customized. It provides excellent thermal insulation with a service life of up to 50 years.
Strength can be enhanced through the use of FRP skin, which has excellent corrosion resistance, weather resistance, and waterproof performance.
Below are their properties:

Structure of fiberglass XPS
XPS foam
XPS stands for Extruded Styrene Foam Board, which has good insulation properties and is used for thermal insulation. It is a rigid closed-cell material that does not absorb water and has a long life.
FRP sheet
FRP is an excellent high-performance material, consisting of glass fiber reinforcement. It has high performance, high strength, and UV resistance.
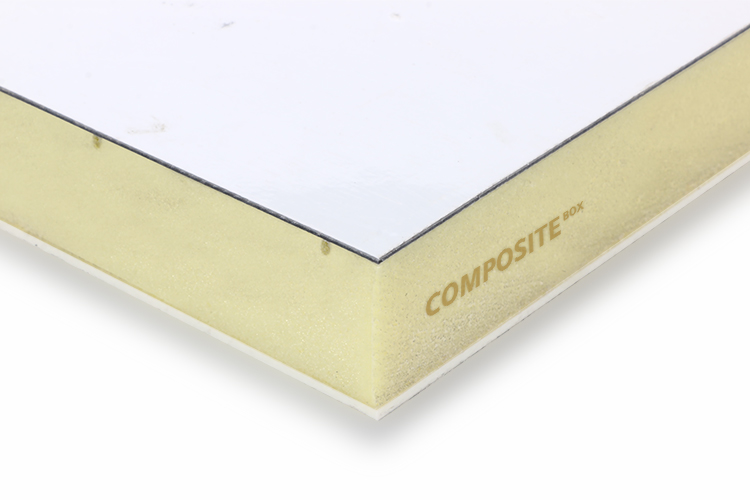
Composite Box
Application of fiberglass XPS panel :
This product is ideal for applications that require thermal insulation properties and waterproofing. For example, interior insulation, building insulation, vehicle insulation, etc.
Product Parameters
Product Specifications
Item | Specification |
---|---|
Skin Material | FRP (Fiberglass Reinforced Plastic), CFRT (Continuous Fiber Reinforced Thermoplastic), Aluminum Sheet, Plywood, Stainless Steel Sheet, Aluzinc Steel, etc. |
Core Material | XPS (Extruded Polystyrene Foam Board) |
Total Thickness | 10~120 mm |
Length Range | ≤12m |
Width Range | ≤3.2m |
Surface Treatment | Glossy, Matte, Embossed, etc. |
Surface Color | RAL Color Series |
Composite Method | Eco-friendly Adhesive |
Processing Method | CNC Machining, Embedded Structure Reinforcement |
Technical Specifications
Item | Specification |
---|---|
Core Density | 30~50 kg/m³ |
Compression Strength | 0.1~1 MPa (depending on core thickness) |
Flexural Strength | 36.966 MPa (Max Load: 2770.659N, Sample Size: 300x100x14 mm) |
Operating Temperature | -50℃ ~ +80℃ |
Waterproof Performance | Excellent, core material has 99% waterproof ability |
UV Resistance | Excellent, FRP skin enhances UV resistance |
Thermal Insulation | Excellent, XPS foam provides superior thermal insulation |
Corrosion Resistance | Excellent, surface treatment enhances corrosion resistance |
Moisture Resistance | Good, XPS foam has excellent moisture resistance |
Expected Service Life | Up to 50 years |
Core Density | 35~55 kg/m³ |
Closed Cell Rate | ≥99% |
Thermal Conductivity | 0.024~0.034 W/m·K |
Water Absorption | ≤1% |
Operating Temperature | -50℃ ~ +80℃ |
why choose us?
Customer Satisfaction
Insisting on high quality products and servers, centered around customer experience
Quality Assurance
We strictly control every production process to bring reliable quality assurance to our customers.
Advanced Production Line
The world’s top production line ensures product precision and efficiency.
Customization
We provide 100% customization, making orders less difficult.